Hydrogen Detectors in Battery Rooms: Types, Uses, Installation
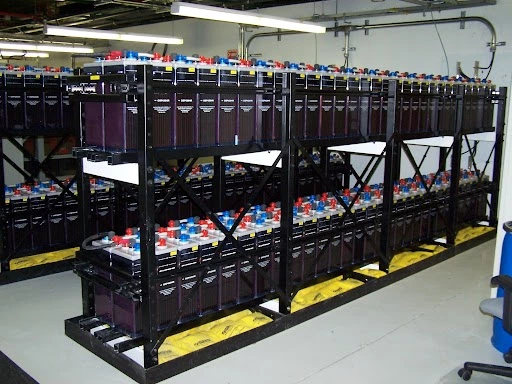
What are Hydrogen Gas Detectors And Their Vital Role?
In the vast landscape of industrial operations, safety is paramount. One of the key elements of ensuring safety in industries where hydrogen gas is used is the hydrogen gas detector. These devices are unsung heroes, quietly but vigilantly monitoring the air for the presence of hydrogen gas and playing a vital role in preventing potential disasters.
Understanding Hydrogen Gas Detectors
Hydrogen gas detectors are specialised devices designed for the precise identification and monitoring of hydrogen gas levels in various environments. These detectors are essential in industries where hydrogen is a crucial component, such as the chemical industry, petrochemical plants, laboratories, and more.
Key Features of Hydrogen Gas Detectors
Hydrogen Gas Detection: Hydrogen gas detectors are tailored to the specific identification of hydrogen gas, providing unparalleled reliability in their detection capabilities.
Real-time Monitoring: These detectors offer real-time monitoring, providing instant data on hydrogen gas concentrations. This feature is invaluable for taking timely action when necessary.
Alarm Systems: Equipped with audible and visual alarms, hydrogen gas detectors ensure that when hydrogen gas levels exceed predefined thresholds, personnel are immediately alerted. This rapid response is vital in preventing potential disasters, as it provides early warnings.
Versatile Applications: Hydrogen gas detectors are adaptable to various environments, making them versatile tools for safety. Whether you're in a chemical plant, laboratory, or any other setting where hydrogen gas is in use, these detectors can be tailored to your specific needs.
Durable Construction: Built to withstand harsh industrial environments, hydrogen gas detectors are designed for long-term, dependable performance, ensuring they operate reliably in challenging conditions.
Safety Compliance: Meeting safety and compliance standards is non-negotiable. Hydrogen gas detectors are designed to meet these standards, offering peace of mind and ensuring the well-being of personnel.
The Vital Role of Hydrogen Gas Detectors
Hydrogen, while essential in various industrial processes, is highly flammable and poses significant risks when its concentration in the air exceeds safe levels. Without the vigilance of hydrogen gas detectors, this invisible threat could lead to explosions, fires, and potentially catastrophic consequences.
The vital role of these detectors lies in their precision in identifying hydrogen gas leaks or abnormal levels. This precision is invaluable in preventing disasters and providing early warnings needed for timely response and intervention.
Hydrogen gas detectors are not only integral to safety but also essential for regulatory compliance. They ensure that industries adhere to safety standards, creating secure working environments and minimising the potential for accidents.
Types Of Hydrogen Gas Detectors
In industrial settings, safety is a top priority. When it comes to monitoring hydrogen gas levels, various types of hydrogen gas detectors play a vital role. Understanding the different types of detectors available can help industries choose the most suitable option for their specific needs.
Catalytic Bead Sensors
Principle: Catalytic bead sensors rely on the catalytic combustion of hydrogen gas. When hydrogen comes into contact with the catalytic bead, it oxidizes, generating heat and altering the electrical resistance, which is then measured.
Applications: These detectors are commonly used in industries where combustible gas leaks may occur, such as oil refineries and chemical plants.
Electrochemical Sensors
Principle: Electrochemical sensors use a chemical reaction to generate an electrical current that is proportional to the concentration of hydrogen gas. They typically consist of a sensing electrode and a counter electrode.
Applications: These detectors are suitable for a wide range of applications, including laboratories, industrial manufacturing, and confined spaces.
Solid-state Sensors
Principle: Solid-state sensors employ a solid-state electrolyte to measure hydrogen gas concentration. They generate an electrical signal that correlates with the concentration of hydrogen.
Applications: These detectors are used in applications where accuracy and stability are crucial, such as in semiconductor manufacturing and aerospace.
Infrared Sensors
Principle: Infrared sensors detect hydrogen gas by analyzing the absorption of specific infrared wavelengths. Hydrogen gas absorbs infrared radiation at characteristic wavelengths, and the change in absorption is used to determine concentration.
Applications: Infrared sensors are often employed in laboratories, pharmaceutical facilities, and research institutions.
Gas Chromatography
Principle: Gas chromatography is a laboratory technique used to separate and analyze gas mixtures. It is highly accurate but generally more complex and not as portable as other detector types.
Applications: Gas chromatography is used in research, quality control, and laboratory analysis, where precise measurement is critical.
Wireless Sensors
Principle: Wireless hydrogen gas detectors are equipped with wireless communication capabilities, allowing data to be transmitted remotely. They can be integrated into larger monitoring systems.
Applications: Wireless detectors are used in applications where real-time data monitoring and remote alerting are essential, such as in large industrial complexes or critical infrastructure facilities.
The Need for Hydrogen Gas Detectors (Associated risk with hydrogen gas)
In the intricate landscape of industrial processes, safety is of utmost importance. One significant aspect of ensuring safety in industries that deal with hydrogen gas is the need for hydrogen gas detectors. These detectors are crucial in mitigating the potential risks associated with hydrogen gas, which is known for its combustibility and flammability.
The Potential Risks of Hydrogen Gas
Hydrogen gas, while essential in various industrial processes, poses unique challenges and potential risks due to its properties:
- Highly Flammable: Hydrogen is highly flammable and can ignite at concentrations as low as 4% in air. Even small leaks can lead to explosive conditions.
- Colourless and Odourless: Hydrogen gas is both colourless and odourless, making it virtually undetectable by the human senses. This lack of sensory cues can lead to unnoticed leaks.
- Lighter Than Air: Hydrogen is lighter than air, which means it tends to rise and disperse quickly. This property can make detecting leaks and identifying their source more challenging.
The Role of Hydrogen Gas Detectors
Hydrogen gas detectors are the unsung heroes in industries where hydrogen gas is used. They play a vital role in identifying, monitoring, and mitigating the potential risks associated with hydrogen gas. Here's how they contribute to safety:
- Early Warning: Hydrogen gas detectors provide early warning by continuously monitoring the environment for hydrogen gas concentrations. As soon as levels exceed predetermined thresholds, these detectors trigger alarms, allowing for swift intervention.
- Preventing Explosions: By promptly alerting personnel to the presence of hydrogen gas, these detectors prevent potential explosions or fires. This early warning is critical for personnel safety.
- Compliance: Many industries are subject to regulatory standards that require the use of hydrogen gas detectors to ensure compliance with safety requirements. These detectors help industries meet these standards.
How to Select the Right Hydrogen Gas Detector
In industrial environments where safety is paramount, selecting the right hydrogen gas detector is critical. With the potential risks associated with hydrogen gas, including its highly flammable nature, it's essential to have the right detector in place.
Understanding Your Requirements
- Application: What is the primary use of the hydrogen gas detector? Is it for a laboratory, chemical plant, petrochemical facility, or another environment?
- Location: Will the detector be used indoors or outdoors? Does it need to withstand harsh environmental conditions?
- Regulatory Compliance: Are there specific safety standards or regulations that your industry must adhere to regarding gas detection equipment?
- Budget: What is your budget for a hydrogen gas detector? Consider the initial purchase cost as well as ongoing maintenance expenses.
- Features: Are there specific features you require, such as real-time monitoring, alarm systems, wireless capabilities, or data logging?
- Alarm Systems: Choose a detector with audible and visual alarms that can alert personnel when gas levels exceed safe thresholds.
- Durability: If the detector will be exposed to harsh environmental conditions, opt for a model with rugged construction.
- Data Monitoring: In today's connected world, consider a detector that offers real-time data monitoring and remote alerting.
- Ease of Maintenance: Evaluate the ongoing maintenance requirements, including sensor replacement and calibration.
Installation Guidelines for Hydrogen Gas Detectors
When it comes to industrial safety, hydrogen gas detectors are indispensable tools for ensuring a secure working environment. However, installing these detectors correctly is just as crucial as having them.
- Select the Appropriate Location: Choosing the right location for your hydrogen gas detector is the first step.
- Proximity to Potential Hazard: Place detectors near areas where hydrogen gas leaks are most likely to occur, such as storage tanks, piping systems, or confined spaces.
- Ventilation: Ensure that detectors are not obstructed by obstacles or placed in areas with poor ventilation, as this could affect their accuracy.
- Follow Manufacturer's Instructions: Always adhere to the manufacturer's installation guidelines. They provide essential information on the ideal positioning, wiring, and calibration for the specific detector model.
- Proper Mounting
Wall Mounting: Wall mounting is common for most hydrogen gas detectors. Ensure that the detector is securely fastened to the wall, away from any potential physical interference.
Ceiling Mounting: Ceiling mounting is suitable for specific applications. When using this method, make sure the detector is securely attached and properly oriented.
4. Calibration and Sensor Placement
Calibration: Calibration is essential to ensure accurate detection. Follow the manufacturer's instructions for calibrating the detector at the recommended intervals.
Sensor Placement: Place the sensor head of the detector at a height and orientation that ensures it effectively monitors the air for hydrogen gas. Follow the manufacturer's guidelines regarding sensor positioning.
5. Wiring and Electrical Connections
Power Supply: Connect the detector to a reliable power source that is protected against power outages and fluctuations. Ensure that the power supply meets the voltage and frequency requirements specified by the manufacturer.
Signal Outputs: Establish proper connections for signal outputs. These may include visual and audible alarms, as well as data transmission systems if your detector is equipped with remote monitoring capabilities.
6. Testing and Commissioning
After installation, perform thorough testing and commissioning. This includes:
Functionality Check: Test the detector's functionality by introducing a small amount of hydrogen gas (if safe to do so) and ensure that the alarm systems trigger as expected.
Response Time: Check the response time of the detector to ensure it reacts promptly to hydrogen gas presence.
Calibration Verification: Verify the calibration settings and adjust them if necessary to maintain accuracy.
7. Regular Maintenance
Routine maintenance is vital to keep your hydrogen gas detector in optimal working condition. Follow the manufacturer's maintenance schedule and replace sensors or components as recommended.
6.Integration with Battery Room Management Systems
In today's rapidly evolving technological landscape, the efficient management of battery rooms is essential for various industries. Battery Room Management Systems (BRMS) play a crucial role in maintaining the integrity of battery systems and ensuring optimal performance.
Battery Room Management Systems: A Quick Overview
Battery Room Management Systems are designed to monitor and manage various aspects of battery rooms, which are commonly found in facilities ranging from data centers to manufacturing plants.
Battery Monitoring: Continuous monitoring of battery parameters such as voltage, current, and temperature.
Data Logging: The ability to record data over time, allowing for trend analysis and performance evaluation.
Alarming: Real-time alerts and alarms for critical conditions, ensuring timely intervention.
Efficiency Optimization: Systems can help extend battery life, reduce energy consumption, and enhance safety.
Compliance: Ensuring compliance with industry standards and regulations, which is critical in sensitive environments like data centres.
Integration with Broader Management Systems
The synergy between Battery Room Management Systems and broader management systems offers several advantages:
1. Enhanced Data Accessibility:
Integration allows the data collected by BRMS to be accessed through central control systems, providing a holistic view of facility operations. This real-time access to battery performance data ensures that any irregularities can be addressed promptly, reducing the risk of critical failures.
2. Predictive Maintenance:
By combining data from BRMS with other facility management systems, predictive maintenance models can be created. This approach optimises maintenance schedules and helps extend the life of batteries, ultimately reducing operational costs.
3. Improved Energy Efficiency:
Integration with building management systems (BMS) or energy management systems (EMS) enables the optimization of power usage, leading to energy savings. For instance, by coordinating the charging and discharging of batteries with peak power demands, facilities can reduce their energy costs.
4. Comprehensive Reporting:
Data from BRMS can be incorporated into facility-wide reporting systems, facilitating compliance reporting, performance analysis, and decision-making.
5. Enhanced Safety:
By integrating with broader safety and security systems, BRMS can help in mitigating risks and ensuring a secure working environment.
6. Streamlined Workflow:
Integration simplifies processes. Alerts and notifications from BRMS can be incorporated into workflow management systems, enhancing operational efficiency.
7. Response Protocols : Alarm Thresholds
In various industries, especially those where safety and security are paramount, the establishment of effective response protocols is critical. Central to these protocols are alarm thresholds, which trigger actions or alerts when specific conditions are met.
Understanding Alarm Thresholds
Alarm thresholds are predefined values or limits that serve as triggers for alarms, notifications, or automated responses. These thresholds are set based on specific parameters or conditions that need close monitoring. Some common examples of alarm threshold parameters include:
Temperature: In a server room or industrial process, high or low temperatures can indicate a problem, prompting the activation of cooling systems or shutdown procedures.
Humidity: Humidity levels are crucial in environments like cleanrooms or manufacturing facilities. Deviations from the defined threshold can trigger alarms for immediate attention.
Gas Concentrations: In facilities handling hazardous gases, such as hydrogen or volatile organic compounds, the concentration of these gases must be monitored. Alarm thresholds ensure rapid response to any hazardous buildup.
Pressure: In pipelines or chemical reactors, pressure changes can signify leaks or operational issues. Alarm thresholds prompt quick responses to prevent accidents.
Voltage or Current: In electrical systems, fluctuations in voltage or current can indicate potential problems. Alarm thresholds enable immediate corrective actions or shutdown procedures.
The Significance of Alarm Thresholds
Timely Detection: Alarm thresholds are a frontline defense mechanism, enabling the timely detection of deviations from desired conditions. Early detection can prevent costly damage or safety hazards.
Safety Assurance: In environments where safety is a priority, such as chemical plants or laboratories, alarm thresholds ensure that safety measures are triggered when conditions become unsafe.
Operational Efficiency: Alarm thresholds help maintain operational efficiency by identifying and addressing issues before they escalate. This minimizes downtime and loss of productivity.
Regulatory Compliance: Many industries are subject to safety and environmental regulations that require the use of alarm thresholds. Compliance is critical to avoid penalties and maintain a good standing.
Data-Driven Decision Making: Alarm thresholds provide valuable data for decision-makers. By analyzing the data generated from alarms, improvements in processes and safety protocols can be made.
Establishing Alarm Thresholds
Setting alarm thresholds should be a thoughtful process that considers the specific requirements and risks of an industry or facility. Factors such as industry standards, regulatory requirements, and historical data should all be taken into account when defining these thresholds. Regular reviews and updates of alarm thresholds are also crucial as technology and industry standards evolve.
8. Battery Technologies and Hydrogen (Types of Batteries Emitting Hydrogen And Mitigating Risk)
Battery technologies have made significant strides in various industries, from powering our smartphones to enabling electric vehicles and renewable energy storage. However, there's one aspect of battery technology that often goes unnoticed: the potential risk associated with hydrogen emission.
Types of Batteries Emitting Hydrogen
Lead-Acid Batteries: Lead-acid batteries are commonly used in applications like automobiles, uninterruptible power supplies (UPS), and forklifts. They produce hydrogen gas during both charging and discharging processes. Overcharging, age, and damage to lead-acid batteries can increase the risk of hydrogen emission.
Nickel-Metal Hydride (NiMH) Batteries: NiMH batteries are found in various portable devices and hybrid electric vehicles. While they produce minimal hydrogen, their potential for leakage or rupture under certain conditions can still lead to gas emission.
Lithium-Ion Batteries: Lithium-ion batteries are ubiquitous in modern electronics and electric vehicles. While they are known for their stability, in rare cases of thermal runaway, they can emit hydrogen gas, posing a safety concern.
Lithium Iron Phosphate (LiFePO4) Batteries: LiFePO4 batteries are increasingly used in renewable energy storage and electric vehicles due to their stability and safety. These batteries have a lower risk of hydrogen emission compared to other lithium-ion batteries.
Mitigating the Risks Associated with Hydrogen Emission
Proper Ventilation: Ensure that areas containing batteries are well-ventilated to disperse any hydrogen gas that may be emitted. Adequate ventilation reduces the risk of gas buildup.
Regular Maintenance: Implement routine maintenance and inspections to identify and address any issues with batteries, preventing the conditions that may lead to hydrogen emission.
Hydrogen Gas Detection: Install hydrogen gas detectors, especially in enclosed spaces or rooms with a high concentration of batteries. These detectors can provide early warnings if hydrogen levels become unsafe.
Temperature Monitoring: Keep batteries within their recommended operating temperature ranges to minimise the risk of thermal runaway, which can lead to hydrogen emission.
Safety Protocols: Develop and communicate safety protocols for handling, charging, and disposing of batteries. Ensure that personnel are trained to follow these protocols.
Safe Battery Technologies: When possible, choose battery technologies with a lower risk of hydrogen emission. Technologies like LiFePO4 are known for their stability and safety.
While battery technologies have revolutionised industries and improved our daily lives, it's essential to be aware of the potential risks associated with hydrogen emission. Understanding which types of batteries emit hydrogen and implementing safety measures to mitigate these risks is crucial.
Mitigating the risks of hydrogen emission is not just about safety; it's also about maintaining the reliability and longevity of battery systems. By following best practices, conducting regular maintenance, and investing in safe battery technologies, we can continue to harness the power of batteries while minimising potential risks.
9. Industry Regulations and Compliance ( Like Safety Standards)
In today's complex and rapidly evolving industrial landscape, safety is a top priority. Ensuring that industries operate safely and securely is a collective effort that involves adhering to industry regulations and compliance standards.
The Significance of Industry Regulations and Compliance
Industry regulations and compliance standards are designed to achieve several essential objectives:
Safety: The primary aim is to safeguard the well-being of workers and the surrounding community. Compliance ensures that hazardous situations are identified and mitigated, reducing the risk of accidents.
Environmental Protection: Regulations are also intended to protect the environment. Compliance standards address issues such as emissions, waste disposal, and resource conservation, ensuring industries operate responsibly.
Consistency: Regulations promote consistency and uniformity in practices, making it easier to assess and improve safety and environmental measures.
Quality Assurance: Compliance often involves quality control and assurance measures to maintain the quality of products and services, which is essential for customer satisfaction and brand reputation.
Safety Standards: A Closer Look
Safety standards, a subset of industry regulations, are particularly vital for protecting lives and assets. These standards encompass a wide range of industries, from construction to manufacturing, and include areas such as electrical safety, fire safety, workplace safety, and product safety. Key aspects of safety standards include:
Risk Assessment: Identifying potential hazards and assessing risks is a fundamental element of safety standards. It involves understanding the risks associated with specific processes, equipment, or products.
Safety Procedures: Safety standards prescribe the use of safety procedures and best practices. These can include safety protocols, emergency response plans, and training requirements.
Safety Equipment: Standards often mandate the use of specific safety equipment, such as personal protective gear, fire extinguishers, or safety interlocks on machinery.
Testing and Certification: Many safety standards require products or equipment to undergo testing and certification to ensure they meet safety requirements.
Compliance Challenges and Benefits
Complying with industry regulations and safety standards can be challenging. It may require investments in training, equipment, and process improvements.
Risk Reduction: Compliance reduces the risk of accidents, injuries, and environmental harm, which can lead to costly legal and financial consequences.
Improved Reputation: Compliance demonstrates a commitment to safety and environmental responsibility, enhancing a company's reputation and trustworthiness.
Legal Protection: Compliance provides legal protection in the event of accidents or disputes, demonstrating that a company has taken due diligence to prevent harm.
Efficiency: Compliance often leads to improved operational efficiency through the adoption of best practices and the reduction of costly accidents and downtime.
10. Ensuring Safety and Efficiency in Battery Rooms ( Your Conclusion + Real Life Examples)
Battery rooms play a critical role in many industries, from data centers to manufacturing plants. They house the power that keeps our operations running smoothly. However, these rooms also come with potential risks, primarily due to the energy stored in the batteries and the gases they emit. In this SEO-friendly blog, we will explore the essential elements required to ensure safety and efficiency in battery rooms, followed by real-life examples showcasing the impact of these practices.
Ensuring Safety and Efficiency in Battery Rooms
Proper Ventilation: Battery rooms must be well-ventilated to disperse any potentially harmful gases that batteries may emit during charging or operation. Proper ventilation reduces the risk of gas buildup and helps maintain a safe working environment.
Hydrogen Gas Detection: Installing hydrogen gas detectors is a crucial safety measure. These detectors continuously monitor the air for hydrogen gas levels and provide real-time alerts if concentrations become unsafe. This early warning system is invaluable in preventing accidents.
Regular Maintenance: Routine maintenance and inspections of batteries are essential to identify and address potential issues. Regular maintenance helps extend the life of batteries, reduces downtime, and ensures operational efficiency.
Temperature Control: Maintaining batteries within their recommended temperature range is vital. Proper temperature control safeguards against potential thermal runaway.
Safety Protocols: Developing and communicating safety protocols for handling, charging, and disposing of batteries is critical. Ensuring that personnel are well-trained in these protocols minimizes the risk of accidents.
Real-Life Examples
Data Centers: Data centers rely on uninterrupted power supplies (UPS) to maintain their operations. Proper safety and efficiency measures in battery rooms are crucial to prevent power outages and data loss. Early warning systems and maintenance routines ensure the reliability of UPS systems.
Manufacturing Plants: In manufacturing plants, batteries power critical machinery and equipment. Efficient battery room management is vital to maintain production schedules and prevent costly downtime. Proper ventilation, safety protocols, and maintenance help ensure smooth operations.
Telecommunication Facilities: Telecommunication facilities depend on backup batteries to provide continuous service. Regular maintenance and gas detection systems protect against power failures, ensuring that communication services remain uninterrupted..
Know the latest trends in IAQ solutions from the Ace Instruments team
Instruments that exceed your technical expectations
Comprehensive and customized IAQ solutions for all applications